Özyeğin University, Çekmeköy Campus Nişantepe District, Orman Street, 34794 Çekmeköy - İSTANBUL
Phone : +90 (216) 564 90 00
Fax : +90 (216) 564 99 99
E-mail: info@ozyegin.edu.tr
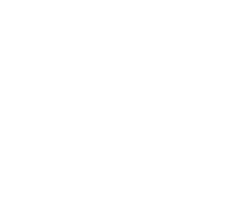
Dissertation Defense - Uğur Şimşek (PHDME)
Uğur Şimşek – Ph.D. Mechanical Engineering
Asst. Prof. Polat Şendur – Advisor
Date: 19.08.2021
Time: 08:30-10:00
Location: This meeting will be held ONLINE. Please send an e-mail to gizem.bakir@ozyegin.edu.tr in order to participate in this defense.
DYNAMIC CHARACTERIZATION AND OPTIMIZATION OF ADDITIVELY MANUFACTURED TPMS LATTICE STRUCTURES
Thesis Committee:
Asst. Prof. Polat Şendur, Özyeğin University
Assoc. Prof. G. Güven Yapıcı, Özyeğin University
Asst. Prof. Ramazan Ünal, Özyeğin University
Assoc. Prof. Güllü Kızıltaş Şendur, Sabancı University
Asst. Prof. Evren Yasa, Eskişehir Osmangazi University
Abstract:
Additive manufacturing has opened new avenues for the manufacturing of structures to achieve challenging engineering tasks. Triply periodic minimal surface (TPMS) lattices, a unique example of such structures, exhibits many attractive properties, such as high stiffness-to-weight ratio and impact characteristics. This thesis focuses on the dynamic characterization and optimization of additively manufactured TPMS lattice structures. In the first part of the thesis, the dynamic performance of a finite element-based model of the gyroid sandwich structure was first validated against the modal testing in terms of its natural frequencies and mode shapes. Subsequently, the effects of the plate and gyroid wall thickness on the dynamic characteristics of the structure were investigated by varying these across their expected limit ranges as part of a parametric study using the validated finite element model. Thereafter, modal characterization of additively manufactured TPMS structures is studied using five different modeling methods for a beam, which is composed of primitive, diamond, IWP, and gyroid unit cells. These methods include (1) shell modeling, (2) solid modeling, (3) homogenization, (4) super-element modeling, and (5) voxelization. The modal characterization is performed by using modal analysis, and the aforementioned models are compared in terms of their computational efficiency and accuracy.
In the second part of the study, a new design methodology using an integrated topology optimization (TO) process is proposed for the development of FGL structures. For that purpose, a material penalization formula derived by the application of homogenization is integrated into the TO process. As a result, relative densities of the TO are mapped directly and radial basis functions (RBFs) are then used to create the geometry of the FGLs efficiently. The proposed methodology is demonstrated in a case study, where a cantilever beam with a desired bandgap characteristic is designed. Moreover, a novel Free-size Optimization based Graded Lattice Generation (FOGLG) method, that generates the functionally graded lattice (FGL) structures using free-size optimization, is proposed. In addition, the reconstruction method suitable for the construction of 3D FGL structures using Additive Manufacturing (AM) is presented. Finally, a hybrid optimization framework is presented to jointly use different surface-based lattices into a design domain to improve the mechanical performance of the lattice structures.
Bio:
Uğur Şimşek received his B.Sc. degree in mechanical engineering from Yıldız Technical University in 2012. He obtained M.Sc. degree in mechanical engineering from Istanbul Technical University in 2016. He is currently working as an advanced lead additive manufacturing engineer at General Electric Aviation (Kocaeli, Turkey), while pursuing the Ph.D. degree in mechanical engineering at the Vibration and Acoustics Laboratory (VAL) at Özyeğin University. His research interests include vibration, structural dynamics, finite element modelling and additive manufacturing.